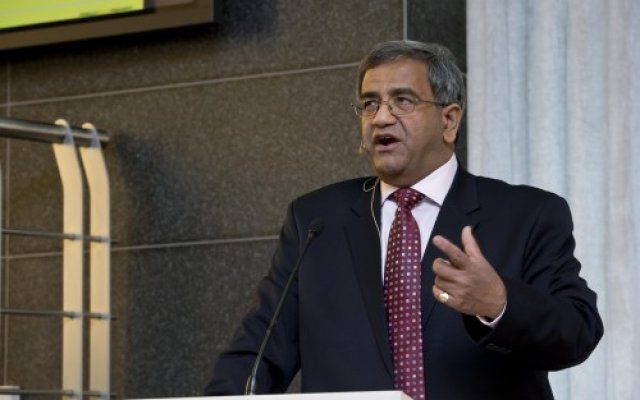
The innovative technology project being undertaken by gold mining company AngloGold Ashanti was continuing to show “pleasing” progress, with the successful deployment of the company’s latest generation reef-boring machine at the company’s TauTona lower carbon leader shaft pillar.
Speaking at Monday’s presentation of yearly and fourth-quarter results, AngloGold COO South Africa Chris Sheppard said that the company was in the process of preparing a reef-boring site at the Savuka carbon leader shaft pillar.
While there had been some setbacks, which was the nature of research and development (R&D) work, the company remained confident that it would get down to the requisite business case that the company had set for reef boring.
On the R&D side, strong stage-gate mechanisms had been put in place to ensure that the company was receiving “the best bang for its buck” and an important aspect was that the “very focused” project management team was fully embedded within Tau Tona’s operational management team. In reply to JP Morgan gold analyst Allan Cooke, Sheppard added that the company was definitely not slowing down its programme but had put its approach with small-diameter machines on hold in the Vaal River area because the nature of the rolling reef meant that it was not drilling out sufficient of the reef band itself.
The technology had thus been changed to that of thermal spawning, which was showing some early success, about which he remained cautiously optimistic. Latest generation reef boring at TauTona had resulted in cycle times improving from 159 hours a hole to performances of 82 hours a hole – closer to the targeted 72-hour blueprint. In a Johannesburg Stock Exchange News Service (SENS) announcement, the company also reported that the ultra-high strength backfill product had also been successfully developed to be able to pump over the required 1 000 m distance, a prerequisite for a full production mining cycle.
The SENS report added that the MK IV machine suffered fourth-quarter regression owing to a change of plan to enforce the use of a contained transport system, which negatively affected the machine’s performance, imposing constraints on the operation of the collector bin and causing shortages in material cars for the transportation of chippings away from the hole. The collector bin had since been redesigned, modified and returned underground for further trials, w
hich were expected to begin in the first quarter of this year with additional material cars having been delivered. The MK III machines drilled 13 holes in the fourth quarter of 2015, during which time rock engineers recommended the suspension of drilling in block 2, resulting in an unplanned move of the Azikohoho machine to the top reef drive of block 7.
Owing to this move, the machine had to be converted to raise-bore mode and the opportunity was also used to install the new mechanical anchoring system for speeding up the set-up times. As part of improving the machine performance, the rod handling system had since been installed on the machine to assist with the installation and removal of the drill rods, scheduled for first-quarter drilling in the Ventersdorp Carbon Reef site. Other MK III machines were expected to be fitted with this system as part of the refurbishment programme.
The new raise-boring technology produced 100 kg of gold for AngloGold Ashanti in 2014 and was targeted to be competitive with conventional mining in 2015. The company has used the raise-bore technology to drill in shaft pillars that are unsafe to mine conventionally. So far, the technology has put the company in a position to mine “all the gold and only the gold all the time” and to overcome the current drill-and-blast constraint of only being able to work 66% of each day.
This resulted in discussion being opened with the union at TauTona to embark on a programme of continuous mining. The idea is to facilitate work to take place 365 days a year, 24 hours of the day. The need for the new technology is compelling as only 60% of the gold ore in South Africa’s rich Witwatersrand basin is accessible using current drill-and-blast technology and 40% of the gold is left behind in pillars to keep seismicity at bay.
The current mining method then loses a further 25% to 30% of that 60% because blasting breaks the ore into so many pieces that not all of them can be recovered, particularly as fractured sizes range from fine powder to large boulders. Once blasted, the product is moved up to seven times, which results in more losses. On average, there is 200% more waste than gold in the mix moved and dilution can be as high as 1 500%, which means that huge volumes of nonpay material have to be transported out of ever-deepening cavities.
One hundred grams of gold in the ground becomes 30 g or 25 g of gold on surface, after getting out only 60% of what was there in the first place. What is far worse is the death and injury rate, which remains in spite of the huge effort to achieve zero fatalities.
During the twentieth century alone, the Leon Commission calculated that 69 000 people were killed in South Africa’s mines and a million seriously injured, maimed or physically damaged. Currently, safety has plateaued and, unless significant change is made to what creates this plateau, death and injury in mines will continue. There is thus an absolute need to change if deep-level gold mining is to be sustainable – and AngloGold Ashanti has been a prime mover in this under senior VP: technology and projects Shaun Newberry.
The current mining method is clearly not the one that should take South Africa into the future. In fact, if it continues to be pursued, gold mining will end long before the Witwatersrand basin’s three-billion ounces of gold are extracted. Some 1.7-billion ounces have been mined, only 200-million more ounces are in reserve and 1.1-billion ounces stand to be left in the ground unless a new mining technology is introduced. Since 2010, AngloGold Ashanti has been working consistently to introduce a safer and more efficient way of mining narrow-reef orebodies and has developed and manufactured prototypes in a relatively short time.
The new technology involves boring holes of the required reef-channel width, collecting and transferring the bored chips in an enclosed system for further processing and backfilling the cavities to stabilise the underground environment and reduce seismicity. In order to reach depths of 5 km and beyond, the rock mass removed needs to be replaced with similar material of 170 MPa compressive strength to prevent movement. Each hole is sealed at the bottom access point and a high-viscosity mixed product is pumped to the top access point.
All this is already happening. Steps are being taken to enable the reef-boring machines already in use to move and align themselves automatically on the basis of geological data. Near-term work is also being undertaken to evolve towards a form of gold liberation using chemicals, thermal energy or other methods, to free the gold for hydraulic transport back to surface and achieve the original vision of having gold on tap 24 hours a day, 365 days a year.
Knowledge of rock fragmentation is also an enabler for reef boring, as less power will be needed if better rock fragmentation methodology can be developed. There are many such projects under way in the background because of their relationship with the programme’s first two stages. But exponentially faster geological information will be needed to deploy the new technology.
To be able to bore the reef over distance, the location of the gold-bearing rock will have to be determined far more quickly and accurately. Currently, there is nothing available that can provide the information at the pace needed and something suitable will have to be developed. In the meantime, the quick win of shaft pillar mining is being seized upon, where such information is already available. High-speed haulage-boring machines are needed to create the main infrastructure for logistics and geological drilling platforms as well as smaller-diameter access for on-reef infrastructure.
Once the on-reef grid has been established, the idea is for ventilation to be achieved by drilling holes between the drives using a raise-bore machine. It is envisaged that reef boring and ultra-high-strength backfilling can then take place from the drives. Reef-boring begins from the bottom reef drive using a machine set up on the lower of the two levels to be connected. Line boring is used to drill a hole from the lower level to the upper level and is then backfilled on completion.
The completed hole has smooth walls and does not require support. The vision is of mechanical mining being remotely controlled from safe areas, and extraction ratios being boosted by a new mining methodology, and backfilling of cavities with material as hard as the rock itself. Targeted are significant portions of orebody currently left behind and the elimination of gold loss down microcracks.
Instead, the plan is to transport consistent smaller chips from the rock face to the mill in one enclosed system. The technology is said to have the potential to increase the extraction ratio from the current 60% to 70% to at least 80% to 90% and will help solve the high closure challenge expected at mining depths of 5 000 m and beyond. Skin-to-skin drilling leaves a wedge of gold that may be recovered by lancing or micro-waving.
The second stage is targeting intelligent mining machines and the third stage a visionary gold-on-tap mimicking of the oil and gas industry. The three cohesive stages of the roadmap aim to bring sustainability to gold mining at ever-increasing depth, with safety, extraction ratio, dilution, mine call factor and asset use coming under the microscope. If the country succeeds in finding a viable new alternative, it would not only be able to mine all remaining pillars and go to the ultradepths, but it could also reopen a large number of closed mine shafts and revive mining ghost towns, which is why the national shoulder needs to be put to the wheel with the utmost vigour.
Source: Miningweekly